The common misconception about a manufacturing building and design often revolves around its perceived simplicity. Many people see these structures as mere warehouses or large sheds where assembly lines churn out products monotonously. However, the reality is far more dynamic.
The interior of a manufacturing building is a complex maze of precision. It houses specialized zones for raw material storage, production lines, quality control, and logistics. The meticulous design of these buildings meet the specific needs of a particular industry, ensuring efficient and safe production operations.
Table of content:
- Understanding the Concept of a Manufacturing Building
- Different Types of Manufacturing Buildings
- Manufacturing Building Design and Layout
- Role of Manufacturing Buildings in the Industrial Sector
- Future Trends in Manufacturing Building Design
- Frequently Asked Questions
Understanding the Concept of a Manufacturing Building
A manufacturing building is a purpose-built facility that houses machinery, equipment, and materials necessary for producing goods. Its primary purpose is to provide a dedicated space for industrial processes.
Manufacturing buildings are vital to the economy as they provide a centralized location for producing goods on a large scale. They streamline the manufacturing process, ensure quality control, and help meet production deadlines.
These buildings are often strategically located near transportation hubs to easily access suppliers and distribution centers.
Key Features of a Manufacturing Building
A manufacturing building incorporates several key features to ensure its functionality and effectiveness. One essential aspect is the availability of ample floor space to accommodate machinery and workflow.
The building also has specialized utilities, such as power supply, ventilation systems, and appropriate infrastructure for handling waste and hazardous materials. Additionally, the layout and design of a manufacturing building prioritize easy access to raw materials, storage areas, and finished product storage or distribution sections.
Another key feature of manufacturing buildings is incorporating safety measures to protect workers and prevent accidents. This includes the installation of safety barriers, emergency exits, fire suppression systems, and proper lighting.
Additionally, manufacturing buildings often adhere to strict environmental regulations to minimize their impact on the surrounding ecosystem. This may involve implementing energy-efficient practices, waste-recycling programs, and pollution-control measures to promote sustainability and eco-friendliness.
Different Types of Manufacturing Buildings
Heavy Industrial Buildings
Heavy industrial buildings are specifically designed for industries involving large-scale manufacturing processes, such as automobile manufacturing, steel production, or heavy machinery fabrication. These buildings have high load-bearing capabilities and sturdy infrastructure to support heavy equipment and machinery.
Heavy industrial buildings often feature specialized ventilation systems to manage the emissions and fumes produced during manufacturing. Additionally, these buildings may have reinforced flooring to withstand the weight of heavy machinery and equipment. The layout of heavy industrial buildings is carefully planned to optimize workflow and ensure the efficient movement of materials and products throughout production.
Light Industrial Buildings
Light industrial buildings are tailored for smaller-scale manufacturing industries, such as electronics assembly or food processing. These buildings are characterized by a more flexible layout and are often modular in design, allowing businesses to adapt their production lines to changing needs and technologies more easily.
Did You Know?
The popularity of steel structures has grown rapidly in the past decade and now accounts for 95% of all new industrial building construction.
Light industrial buildings typically prioritize energy efficiency, with natural lighting and insulation features to reduce energy consumption. These buildings may also include dedicated spaces for quality control and testing to ensure that products meet industry standards.
The layout of light industrial buildings is designed to facilitate the smooth flow of materials and components, enhancing productivity and minimizing bottlenecks in the production process.
Flex Industrial Buildings
Flex industrial buildings are a hybrid concept that offers versatility to accommodate manufacturing and warehouse functions within a single space. These buildings provide the flexibility to switch between production and storage activities, making them ideal for businesses with varying production volumes or inventory requirements.
Flex industrial buildings often feature adjustable partition walls and mezzanine levels to create separate zones for manufacturing and warehousing activities. These buildings may also include loading docks and drive-in doors to facilitate the movement of goods in and out of the facility.
The layout of flex industrial buildings is designed to maximize space utilization and operational efficiency, allowing businesses to optimize their production and storage processes seamlessly.
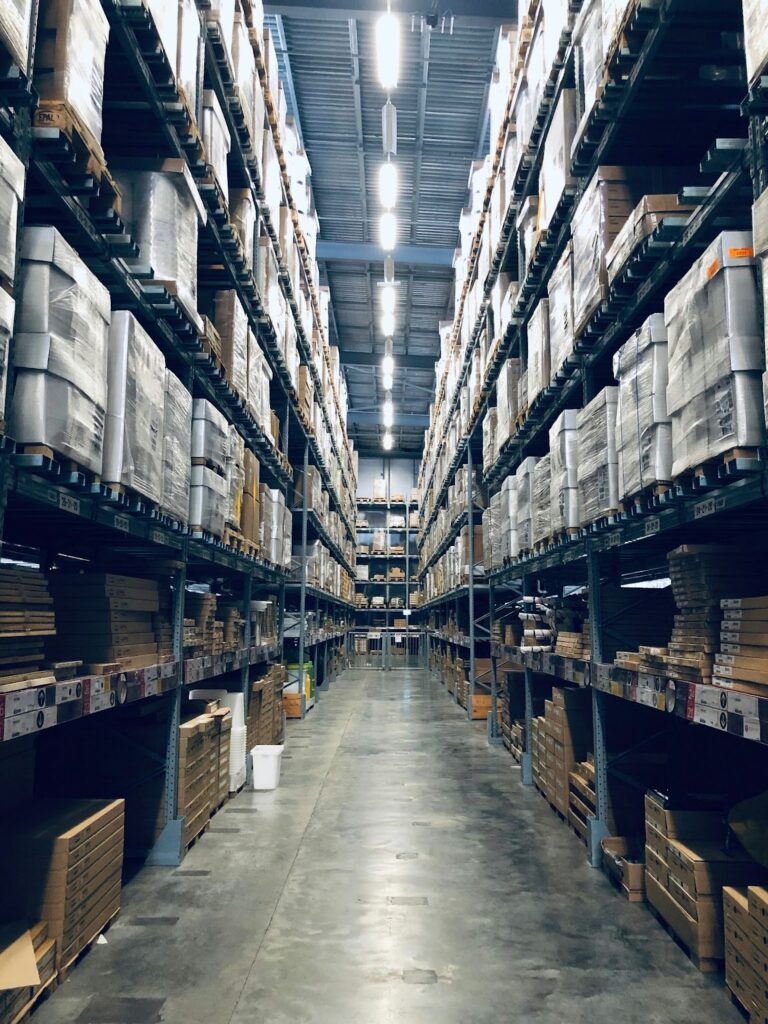
Manufacturing Building Design and Layout
Importance of Efficient Design
Efficient manufacturing building design is important as it directly impacts productivity, safety, and overall operational costs. Carefully plan the layout to optimize workflow, minimize material handling distances, and ensure a logical progression of production activities.
A thoughtfully designed manufacturing building can significantly enhance productivity by reducing production bottlenecks and minimizing unnecessary downtime.
Moreover, an efficient design can also improve employee morale and satisfaction by creating a well-organized and safe working environment.
By considering factors such as ergonomics, lighting, and ventilation, the design can enhance worker comfort and reduce the risk of workplace injuries, ultimately leading to a more engaged and productive workforce.
Essential Components of a Manufacturing Building Layout
In a well-designed manufacturing building, the layout typically includes distinct areas for receiving materials, production lines or workstations, quality control, storage, and shipping.
Strategically positioning each area facilitates the smooth flow of materials and minimizes time wastage. Adequate space is allocated for the storage of raw materials, work-in-progress inventory, and finished goods, ensuring efficient logistics within the building.
Furthermore, the layout should also incorporate designated spaces for maintenance activities and equipment storage to ensure that machinery is properly maintained and readily accessible.
By integrating maintenance areas into the overall design, manufacturing facilities can streamline maintenance processes, reduce downtime due to equipment failures, and prolong the lifespan of critical machinery.
Role of Manufacturing Buildings in the Industrial Sector
Manufacturing buildings are the backbone of the industrial sector. In addition to providing a dedicated space for manufacturing activities, these buildings house cutting-edge technology and equipment essential for modern production methods.
Furthermore, manufacturing buildings are not just structures; they are strategic assets that contribute to the overall competitiveness of a company. Companies invest in state-of-the-art facilities to stay ahead of the competition, improve product quality, and meet the ever-evolving demands of consumers.
Impact on Production Processes
Manufacturing buildings are essential for the effectiveness of production operations. They offer a specific area that allows businesses to function at a larger scale, optimize their operations, and utilize specialized tools and machinery.
Additionally, the manufacturing building design and layout are carefully crafted to enhance material flow and minimize any production delays. Well-planned layouts, strategically positioned storage spaces, and clearly designated working areas substantially augment the productivity of the manufacturing process.
Consequently, many businesses prefer steel constructions over other options because they eliminate the requirement for internal support, granting the flexibility to customize the interior space according to their specific needs.
Influence on Worker Safety and Productivity
Manufacturing building design and layout significantly impact worker safety and productivity. Well-designed buildings prioritize safety features such as proper ventilation, effective lighting, and smooth traffic flow to minimize accidents and promote a healthy work environment.
Additionally, the layout should minimize unnecessary movement and provide ergonomic workstations, enhancing worker comfort and productivity.
Employees feeling safe and supported in their work environment boosts their morale and overall job satisfaction.
Furthermore, manufacturing buildings incorporate advanced safety systems and protocols to ensure the well-being of workers. Automated emergency response mechanisms and stringent safety training programs equip these buildings to handle any unforeseen circumstances and protect the workforce from potential hazards.
Future Trends in Manufacturing Building Design
Sustainable and Green Building Practices
The future of manufacturing buildings lies in sustainable and green building practices. These buildings will increasingly incorporate energy-efficient design, including the use of renewable energy sources, efficient insulation, and advanced waste-management systems. Employing sustainable building practices not only reduces environmental impact but also offers long-term cost savings through decreased energy consumption and improved resource utilization.
One example of sustainable building practices is the use of solar panels to harness the power of the sun and generate clean electricity. These panels, integrated into the building’s design as rooftop installations or as part of the building’s facade, can significantly reduce manufacturing buildings’ reliance on traditional energy sources, leading to lower carbon emissions and a smaller ecological footprint by utilizing solar energy.
In addition to energy efficiency, green building practices also focus on water conservation. Manufacturing buildings can incorporate rainwater-harvesting systems, which collect and store rainwater for various uses, such as irrigation or cooling systems. By reducing the demand for freshwater, these systems contribute to the overall sustainability of the building and help conserve this precious resource.
Did You Know?
Steel being 100% recyclable makes it eco-friendly. Recycled Steel leaves no waste product, and retains its original properties.
Technological Innovations in Manufacturing Building Design
Technology advancements will continue to shape the design of manufacturing buildings. To improve production efficiency and accuracy, building systems will incorporate automation, robotics, and artificial intelligence.
Smart manufacturing buildings will incorporate sensors and data analytics to optimize workflows, monitor equipment health, and improve predictive maintenance. These innovations will revolutionize the manufacturing industry, leading to higher productivity, shorter lead times, and increased competitiveness on a global scale.
One exciting technological innovation in manufacturing building design is the implementation of 3D printing. This cutting-edge technology allows for creating complex and customized parts directly on-site, eliminating the need for traditional manufacturing processes and reducing waste.
3D printing can also enable rapid prototyping, allowing manufacturers to quickly iterate and improve their designs, ultimately leading to more efficient and cost-effective production.
Furthermore, integrating virtual reality (VR) and augmented reality (AR) technologies in manufacturing building design offers exciting possibilities. VR can simulate and optimize production workflows, allowing manufacturers to identify potential bottlenecks or inefficiencies before constructing the building. AR, on the other hand, can provide real-time information and guidance to workers, improving their productivity and reducing errors.
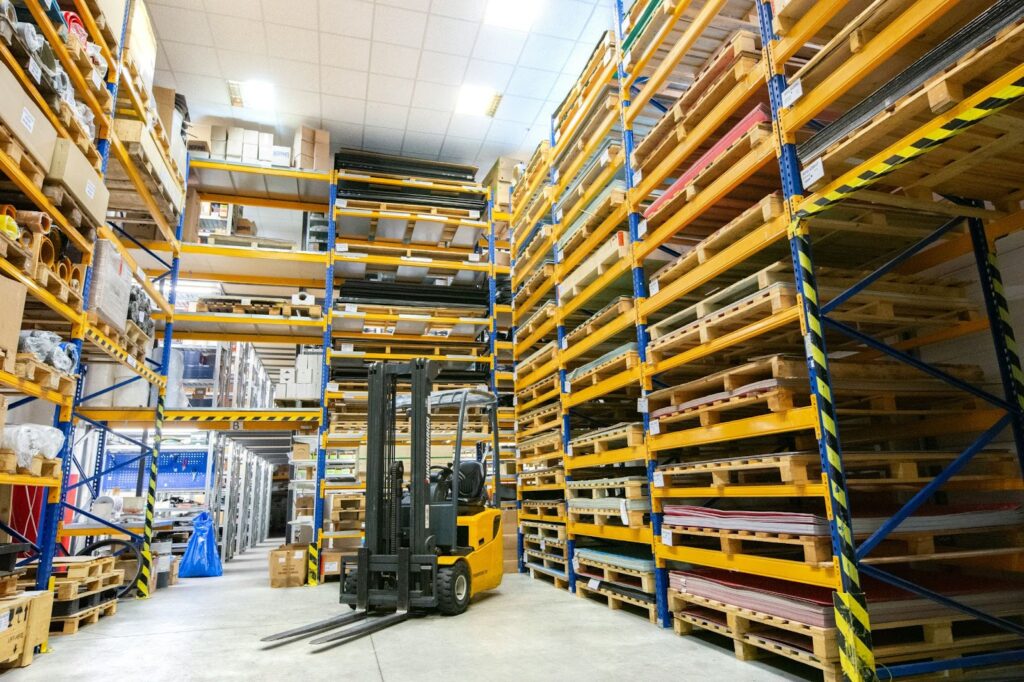
Conclusion
Manufacturing buildings are vital for the industrial sector, providing dedicated spaces for efficient production processes.
These buildings are made to meet the special needs of different industries. They are designed to make work easier, safer, and more productive. This helps businesses do well in the manufacturing world, which is always changing.
Looking ahead, sustainable practices and technological advancements will shape the future of manufacturing building design, making them more sustainable, efficient, and customizable to the changing needs of industries.
SteelCo has been designing and delivering industrial buildings for over 20 years. Our team of experts with 100+ years of industry experience ensures you receive inspiring solutions with industry-leading service levels, project support, and turnaround times. Learn more about us.
Frequently Asked Questions
What is a manufacturing building construction cost?
The construction cost of a manufacturing building can vary widely, depending on several factors such as type, size, location, materials used, and specific needs of the production process. Generally speaking, construction costs can range from $50 to $250 or more per square foot. These figures are broad estimates and can significantly fluctuate based on the client’s customization, the cost of labor in the area, and the price of raw materials at the time of construction.
What is a common misconception about manufacturing buildings?
Many people mistakenly think manufacturing buildings, particularly those made of steel, are weak or flimsy due to their lightweight construction. However, steel buildings are incredibly strong and durable, capable of withstanding severe weather conditions, including hurricanes, without losing their structural integrity.
How do manufacturing buildings adhere to environmental regulations?
They may implement energy-efficient practices, waste-recycling programs, and pollution-control measures to minimize impact on the environment and promote sustainability.
What are the types of manufacturing buildings?
Among the diverse types of manufacturing buildings, three prominent categories stand out: Heavy Industrial Buildings, Light Industrial Buildings, and Flex Industrial Buildings. Each category serves distinct purposes and possesses unique characteristics.
How do light industrial buildings differ from heavy industrial buildings?
Light industrial buildings cater to smaller-scale manufacturing, like electronics assembly or food processing, with a more flexible layout and often modular design, prioritizing energy efficiency and adaptable production lines.
How has the popularity of industrial steel structures changed in recent years?
The popularity of industrial steel structures has surged, now accounting for 85% of all new commercial construction, thanks to their adaptability and efficiency in meeting various industrial needs.
What are the cost considerations to keep in mind when building a manufacturing building?
When planning to build a manufacturing building, several cost considerations must be kept in mind to ensure a successful and financially viable project. These considerations include land acquisition cost, construction costs, design and architecture fees, infrastructure and utilities, permitting and compliance costs, technology and machinery, Safety Measures, Environmental and Sustainability Measures, Future Expansion or Modification and operational costs.
Why Is A Metal Building Ideal For Manufacturing Facilities?
Metal buildings offer a range of advantages that make them a popular choice for a variety of construction needs, particularly in the industrial, commercial, and agricultural sectors. Some of the key benefits are:
- Clear Span Construction
- Inexpensive but sturdy
- Easy to budget for
- Less maintenance
- Learn more here
What zoning regulations apply to manufacturing buildings?
Zoning regulations for manufacturing buildings are established by local governments and can vary significantly depending on the jurisdiction. Some common zoning categories and considerations include Light Industrial (M-1, LI, etc.), General Industrial Zoning (I-2 or M-2), Heavy Industrial Zoning (I-3 or M-3) etc. Contact your local planning department for detailed information on a specific area’s zoning.